Stable, Like a CAMEL
Important Notice:
Our company name is "Shenzhen Camel Die".
Please note that "Camel Die" is a separate entity and is not affiliated with us in any way. Our email address is @cameldie.com
We urge our customers and partners to verify the correct contact information to avoid any confusion or miscommunication.
Die Casting vs Permanent Mold Casting
The main methods of producing aluminum parts are sand casting, permanent casting, and die casting. Among them, die casting and permanent mold are often confused.
Die casting vs permanent mold casting
Die casting and permanent mold casting use steel molds to form a cavity that contains molten aluminum during cooling. this process is different from the sand mold & sand technology process where a new cavity is formed in the sand mold every cycle. Mold abrasive coating protects the steel from molten metal.


Compared with gravity casting permanent, when using die casting, metal is pressed into the mold cavity under pressure. This makes it very similar to plastic injection molding. Once the metal solidifies, the mold and removal the mold will open.
The major difference between the two steel dies techniques is how the metal gets into the tooling.
In the permanent mold, the metal flows into the cavity from the reservoir. A gate controls the flow speed to reduce turbulence.
Usually, the mold is designed to fill the riser from the bottom of the side so that the riser is at the highest point. After filling, the metal is given time to freeze before the mold is opened and the part removed. Features such as internal galleries are created by placing inserts into the mold before it is closed.

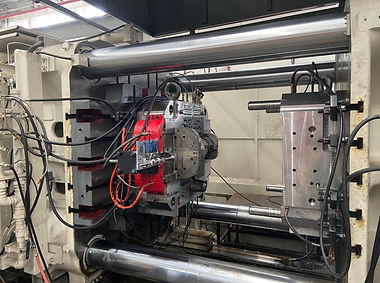
Die casting advantages
Excellent casting surface finish, more than 125 microinches. It may require little or no secondary processing and finishing.
Very tight geometric tolerances can be maintained, including thin walls.
Compared with permanent mold, parts to parts processing speed is faster, which helps reduce the unit cost of long-term operation. Equipment usually requires less floor space.
Die casting molds are often less expensive than permanent casting molds, but the process can produce more precise parts with thinner walls and smoother surfaces.
Common casting metals are aluminum, magnesium, and zinc alloys.
Permanent mold casting advantages
Permanent mold casting is usually lower than the required complexity of the mold, so the price is cheap. Surface finish is typically in the range of 125 to 300 microinches, which means that most secondary processing is required.
The most common process uses gravity to fill the mold, however, gas pressure or a vacuum is also used.
