Stable, Like a CAMEL
Important Notice:
Our company name is "Shenzhen Camel Die".
Please note that "Camel Die" is a separate entity and is not affiliated with us in any way. Our email address is @cameldie.com
We urge our customers and partners to verify the correct contact information to avoid any confusion or miscommunication.
How To Choose Steel For Die Casting Molds
What feature of die casting mold steel?
Die casting mold steel has the characteristics of high production efficiency, short production process, high casting finish and strength, less machining allowance, and metal material saving. It can produce a good surface and internal quality stably and efficiently.
The mold material is required to have high strength, hardness, and thermal stability, especially high thermal strength, thermal fatigue, toughness and wear resistance. Die casting mold generally use hot mold steel H13, SKD61, 8407, 8418.
We recommend the steels from these two companies:
https://www.lkm.com.cn/tool_steel_advantage.php
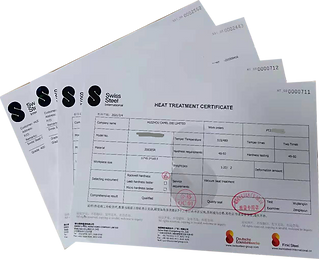
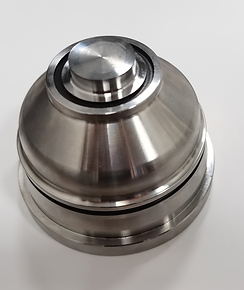
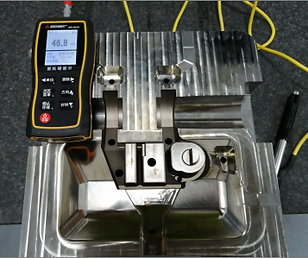
The following requirements when selecting die casting mold steel:
Working conditions of the die casting mold
-
The working conditions of die-casting molds are very harsh compared with other molds. Because of different die-casting metals, they have to withstand a high pressure of 150-500MPa.
-
It is often in contact with molten metal at 300℃~1000℃ when working, and the pouring temperature of different die-casting alloys is also different. And the heating and cooling are repeated continuously, and the temperature gradient along the cross-section is very large.
-
When the mold cavity with molten metal injected at a high speed of 150m/s~70m/s, severe wear will occur.
-
Under the action of liquid metal erosion, the metal is easy to adhere to the surface of the mold cavity, and even penetrate into the mold surface to corrode the mold.
Other requirements of die casting mold steel
Pressure casting can cast parts with complex shapes, high precision, small surface roughness, and good mechanical properties. Therefore, the die-casting mold steel should have the following requirements as below:
-
Greater high-temperature strength and toughness
-
Excellent high temperature wear resistance, oxidation resistance, and tempering resistance stability
-
Good thermal fatigue performance
-
High resistance to melt damage
-
Good hardenability, small heat treatment distortion
-
Good machinability and grinding properties
-
The internal structure of the material is uniform without defects
Principles for the selection of die casting mold materials
-
It can meet the requirements of the working conditions of the die-cast material.
-
The mold size is determined according to the size of the die-cast part.
-
Large and medium-sized precision die-casting molds should be made of steel with good processing performance, reliable performance, and long mold life.
H13 die casting mold steel
H13 is hot die steel, which is formed by adding alloying elements on the basis of carbon steel. H13 die steel is used to manufacture forging dies with high impact load, hot extrusion dies, precision forging dies; die-casting dies for aluminum, copper, and their alloys.
8407 die casting mold steel
8407 is mainly used for various metal die-casting molds, high-quality plastic injection molds. Such as engine molds, automobile lamp molds, etc. In die-casting molds, 8407 steel can be used for mold inserts, cores, cavities, gates, plungers, sleeves, etc.
ASSAB 8407
The advantages of 8407: excellent thermal shock resistance and crack resistance, high-temperature strength, regardless of size, toughness, and ductility, high isotropy, excellent workability, and polishability, excellent hardenability, good heat treatment size Stability, and improvement of mold life.
SKD61 die casting mold steel
SKD61 has good toughness and high-temperature fatigue resistance, can withstand temperature fusion, is suitable for long-term work at high temperatures, and has good cutting performance and polishing performance. It is suitable for making aluminum, zinc, copper alloy die-casting molds, etc.; it is an ideal material for making ejector pins and barrels.
8418 die casting mold steel
8418 has excellent resistance to thermal fatigue cracking, thermal shock cracking, thermal wear, and plastic deformation. These unique properties make it the best choice for die-casting die steel. Used for zinc, magnesium, aluminum, titanium alloys die casting mold, etc.
ASSAB 8418 has the following characteristics:
1. Excellent toughness, ductility, and homogeneity
2. Excellent anti-tempering softening performance
3. Excellent high-temperature strength
4. Excellent hardenability
5. Excellent heat treatment dimensional stability and plating performance
How to improve mold life of die casting mold steel:
1.After heat treatment, the die-casting mold steel can ensure its required strength, hardness, stability, thermal fatigue resistance, and material cutting performance.
2.Strengthening the surface of die-casting die steel is currently the most effective way to extend the mold life of die-casting die steel. There are three main types of surface strengthening:
-
It is not changing the surface chemical composition, laser phase change hardening, etc.
-
It is changing the surface chemical composition, nitriding, etc.
-
It is forming a covering layer on the surface, processing by vapor deposition technology, etc. By adjusting the general heat treatment process, the strength and toughness of steel can be effectively improved, and the mold surface can be given high hardness, wear, and corrosion resistance, seizure resistance, low friction coefficient, and many other excellent properties, so that the service life of die casting mold steel can be increased several times or even dozens of times.