The cross sprue is the passage from the end of the straight sprue to the front of the inner gate; sometimes, the cross sprue can separate into the main cross sprue and the transition cross sprue.
The Cross Sprue Should Conform To The Following Requirements
1) Providing a stable flow of metal fluid.
2) Providing less resistance to the flow of the metal fluid.
3) Low amount of gas encapsulated in the metal fluid during the flow.
4) Provide suitable conditions for the heat balance of the cavity.
5) Make the metal liquid have a suitable solidification time, not hinder the transfer of complementary shrinkage pressure, and not extend the cycle of die-casting.
6) Heat loss should be minimized when the metal liquid flows through the cross sprue.
The Layout Of Multi-cavity Cross Sprue
The production of large and complex die casting, mainly using single-cavity die casting dies. While the shape of the simpler small dies casting and the production batch is more significant, to improve the efficiency of die casting production, reduce the total mold cost. Usually, using multi-cavity die casting dies. Multi-cavity die casting mold cavities can set the same but also can select different types.
A mold multi-cavity die casting mold layout form of the cross sprue should be depending on the layout of each cavity. The structure of the multi-cavity position should base on the structural characteristics of each die casting, the flow condition of the metal liquid, and the heat balance of the mold temperature so that each cavity of the die casting process conditions as far as possible to achieve consistent.
The Layout Forms Of Multi-cavity Cross Sprue Are Rough As Follows
1) Straight-line arrangement
In general, when the metal press into the sprue, the metal liquid starts to divide, and the mainstream of the metal liquid flows forward. In contrast, a small stream of metal liquid flows from the transition cross sprue into the nearest cavity under a slight overpressure to form a pre-filled state. This situation repeats—the results in a small amount of fluid flowing into each cavity. When the mainstream of liquid metal reaches the front of the central cross sprue, the corresponding impact pressure generates, and the cavities fill in turn from top to bottom. Because the pre-filled metal liquid is in a minimal force into the cavity, and in an instant, its temperature will have a significant reduction or even close to the cooling state when they are not easy to fuse with the later entry of the mainstream metal liquid. This filling time difference will make the die casting molding effect reduce; close to the direct sprue die castings are usually easy to produce die-casting defects.
2) Symmetrical arrangement
Symmetrically arranged cross sprue could use for larger die castings. The metal liquid pressed in from the straight sprue enters the cavity through the evenly bifurcated cross sprue. It can ensure that the double cavities have the same die casting process conditions, the mold body is also more balanced force.
3) Comb-style arrangements
The comb arrangement cross sprue has the characteristics of the comb inner gate and the T-shaped cross sprue.
4) Surrounding arrangement
The layout of each cavity is the same as the distance of the straight sprue; the cross sprue can arrange in the form of surround. This arrangement makes the metal liquid flow into each cavity under the same die casting condition, satisfying the principle of filling and cooling simultaneously.
5) Other forms of arrangement
Depends on the structure of die casting, the layout of the multi-cavity mold cavity and the cross sprue also varies. The arrangement of the cross sprue is generally flat and branching, oblique branching, and circular branching. In practice, it depends on the structural characteristics of the die casting.
What Are The Key Factor For Productivity And Part Quality?
In the Die casting process, It is the Die that is key for productivity and part quality.
Not only precision and dimensional accuracy is needed to produce high-quality castings efficiently.
Especially in the casting, runner design and heat energy control prove to be essential factors for achieving the highest productivity and part quality. The CAMEL's job is to develop and build dies that support best-in-class cycle-time, part quality, and die-life.
Tempering must be done before the mold trial to guarantee the die-life.
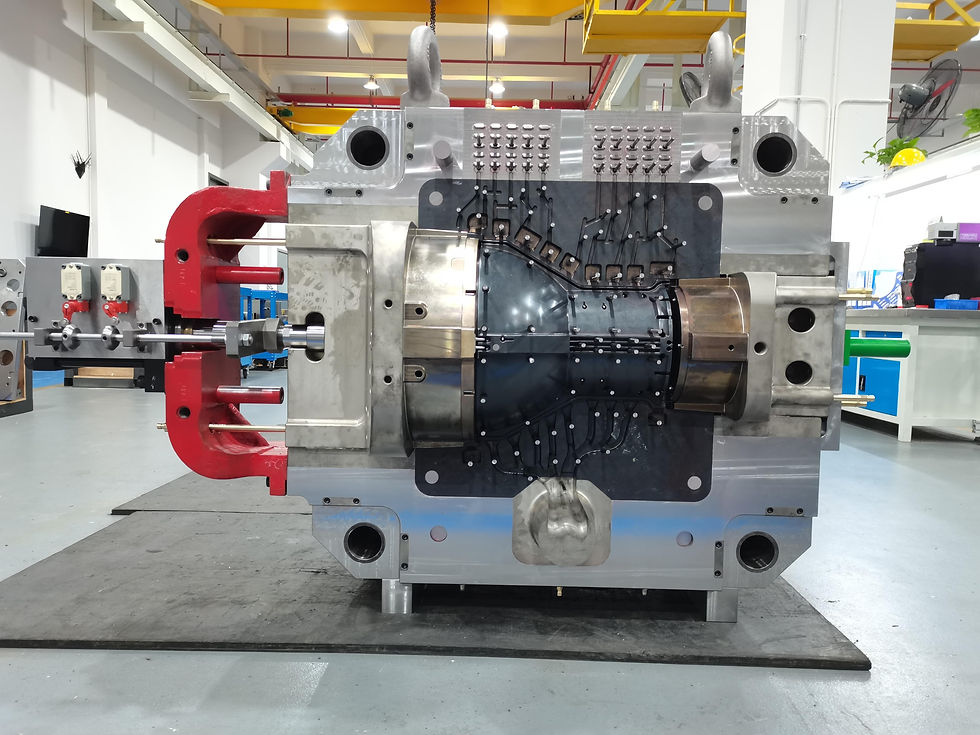

LINK TO:
1, Structure, classification, and design of pouring/gating systems
2, Maintenance of die casting mold
3, Working principle of the die casting mold
4, Mold debugging
5, Temperature controller for Die-casting Production
6, The CASINO Machine Parts in Bulgaria made by CAMEL Manufacture
Comments