Elements of Die Castings Structure Design
- mkt8280
- Sep 3, 2021
- 3 min read
In addition to the quality of die casting is affected by a variety of process factors, the structural design of its parts is also a very important factor, its structural rationality and process adaptability determine whether the subsequent work can be carried out smoothly. Die-casting production technology problems encountered, such as the selection of the parting surface, the design of the sprue, the layout of the launch mechanism, the mastery of the shrinkage law, the guarantee of precision, the type and degree of defects are related to the die-casting process of the die casting itself.
1, Die-casting Process Requirements For Die Casting Structure.
Design die casting in addition to structure, shape, and other aspects have certain requirements, but also should make die casting adapt to the die-casting process. Die casting structure design directly affects the die casting mold structure design and manufacturing of the degree of difficulty, productivity and mold life, and many other aspects, so the design of die casting must emphasize the cooperation between the designer and die casting process personnel, so that die casting in the die casting process may appear many unfavorable factors to be considered in advance and to be excluded. If the designer is also familiar with the die-casting process, then the design of the structure of the die casting is usually more reasonable. The requirements of the die-casting process for die-casting structure design are as follows.
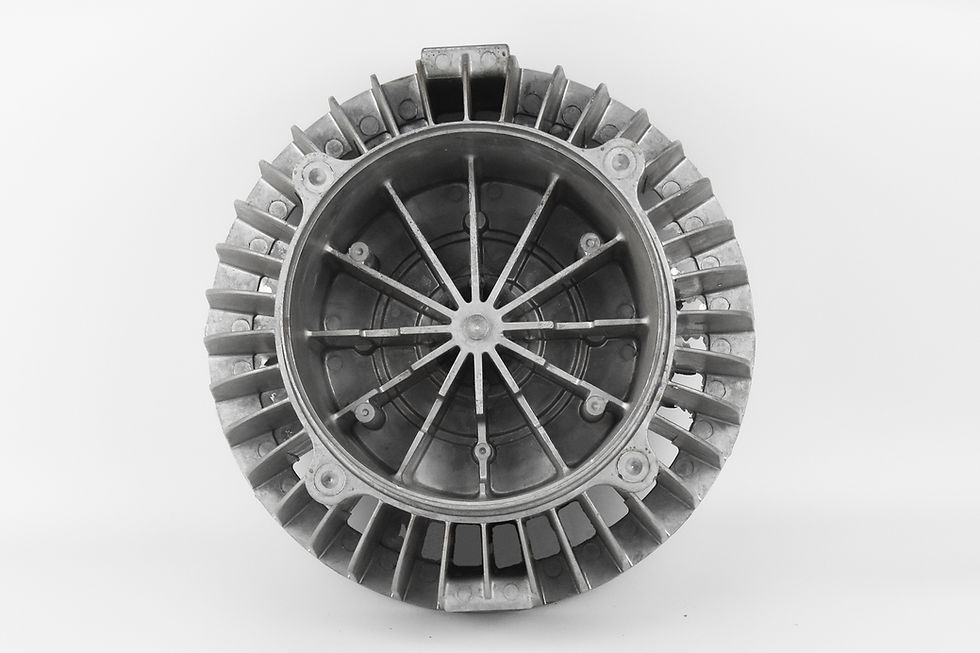
Requirements
To be able to easily remove the die casting from the mold;
To try to eliminate the side concave, deep cavity;
To minimize the core extraction part;
To eliminate the crossed parts of the mold core;
The wall thickness should be uniform;
To eliminate sharp corners.
Description
All the obstacles that are not conducive to the die casting out of the mold should try to eliminate in advance when designing the die casting;
Internal side concavities and deep cavities are the biggest obstacles to mold release. When it cannot be avoided, it should also facilitate the extraction of cores to ensure that the die casting can be removed from the die casting mold smoothly;
Each additional core extraction makes the mold more complex and increases the risk of mold failure;
When the core crosses, not only make the mold structure complex but also prone to failure;
When the wall thickness is not uniform, the die casting will have shrinkage deformation due to the different solidification rates and will produce internal shrinkage and pores, and other defects in the thick part;
Reduce casting stress.
1.1 die casting should simplify the mold structure, extend the life of the mold.
1) design die castings as far as possible to make the parting surface simple;
2) to avoid partial thinning of the mold, to ensure that the mold has sufficient strength and rigidity;
3) to prevent the die casting deformation.
2, The Structure Of The Die Casting Process Elements
The basic structural process elements of die casting include wall thickness, ribs, casting holes, casting rounding, release slope, thread, gear, slot gap, rivet head, convex pattern, mesh, text, logo, pattern, embedded casting, etc.
2.1 Wall thickness and rib design
Die casting reasonable wall thickness depends on the specific structure of the casting, alloy properties and die-casting process, and many other factors. The practice has proved that, as a rule, the mechanical properties of die casting with the increase in wall thickness and decrease. Thin-walled castings than thick-walled castings have higher tensile strength and denseness, thin-walled die casting wears resistance is also good. Die castings with the increase in wall thickness, its internal porosity, and loosening and other defects also increased, so in order to ensure that die castings have sufficient strength and stiffness of the premise, a reasonable wall thickness should be designed into a thin wall and uniform wall thickness, otherwise, it will lead to the uneven internal organization of die castings, but also to the implementation of the die-casting process increases the difficulties. In the usual process conditions, the wall thickness of the die casting should not exceed 4.5mm, the maximum wall thickness and minimum wall thickness ratio should not be greater than 3:1.
The thick wall of the die casting, in order to avoid defects such as sparse, should be thinned wall thickness and additional reinforcement ribs.
"Thank you for this insightful blog; the information regarding Aluminium Pressure Die Casting Tool Design in India is so useful!"
This explanation on Aluminium Pressure Die Casting Tool Design in India simply nails the critical factors for successful die casting. Pay attention to important things: easy release from the mold, uniform wall thickness, and avoiding problematic features like deep cavities, and you will be far more likely to realize quality castings. These can be mainly achieved by simplifying the structure of the mold and through coordination with the engineers. Simple but valuable tips to definitely help out any person working on Aluminium Pressure Die Casting Tool Design, and thus making an incredible difference in the production of stronger, more reliable…