How to Make Die Cast Molds?
- Wilson_CAMEL
- Jul 9, 2021
- 2 min read
Updated: Jul 27, 2021
The standardized mold production process is one of the core competitiveness in mold manufacturing.
From mold order to mold output, it takes about dozens of steps; The key steps of making die cast molds organized are as follows.
Order Preliminary Review → Final Mold Structure Review → Design Review Of Die Casting Mold; Design Review Of Trim Mold → Manufacturing Review → Mold Components Inspection; Mold Steel Hardness Inspection → Mold Base Inspection Report → Cavity & Core Inspection After CNC → Mold Electrode Inspection → Cavity & Core Inspection After Wire Cut → Cavity & Core Inspection After EDM → Mold Pre-Assembly Inspection → Trial Review → Sample Inspection Report → Die Casting Die Checking List → Trim Die Checking List; Inspection Qualified Notice
Design Review Of Die Casting Mold
In the molding process, it is the Die that is key for productivity and part quality. Both precision and dimensional accuracy are needed to efficiently produce high-quality castings. Particularly during the casting process, the runner design and heat energy control prove to be essential factors for achieving the highest productivity and part quality.
It is the CAMEL’s job to develop, and build dies that support best-in-class cycle-time, part quality, and die life. Tempering must be done before the mold trial to guarantee the die life.
Before mold production, The design of die casting dies is also a top priority.
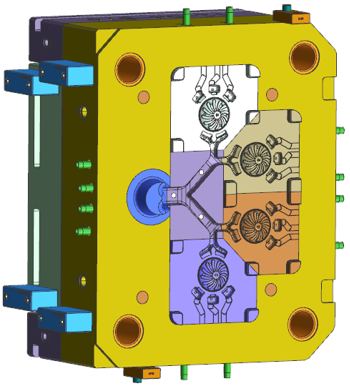
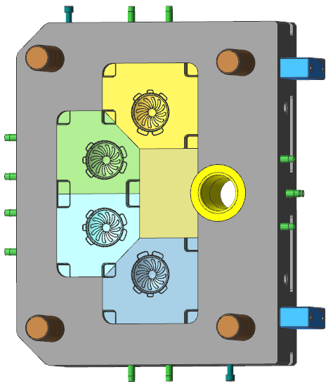

We always do flow simulation by designing many kinds of runner layouts to get the best productivity and part quality. This way most of our die casting dies can be sampled successfully the first time.
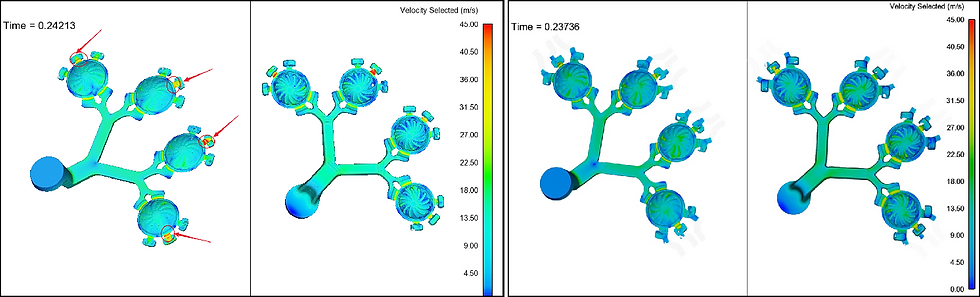
The preliminary flow simulation below appears to show that the overflow speed is too fast and may cause a high risk of mold flush issues. We reduced the area of overflow to control the speed and ensure a better cast and mold quality.

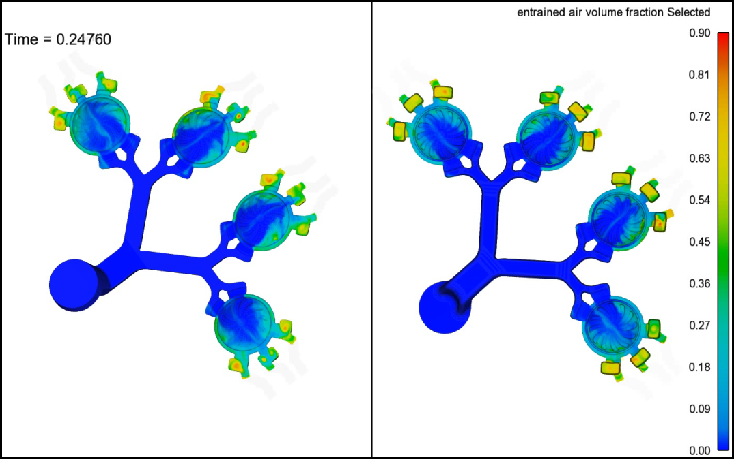
Balanced Heat Energy
CAMEL designs ample cooling lines to control the heat energy balance to get the best cycle-time and part quality. The balanced heat energy also lowers the risk of die cracking.


Die Casting Parts
Overflow is the essential factor for achieving the best part quality. We design all venting separately to ensure that venting can run smoothly and efficiently. This way parts will have a much lower risk of cold lap issues.
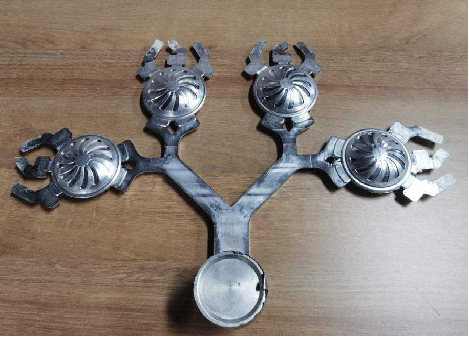

Multi-cavity Trim Dies
Trim dies are indispensable tools for high quantity production. Unprofessional mold makers need to adjust the multi-cavity trim die many times by welding.
CAMEL designs all support blocks, cutters, guide pins, and guide bushes separately for each cavity. We also design separate locating components to control the runner deformation.
This way most of our multi-cavity trim dies can be trimmed successfully the first time.


LINK TO:
Comments