Optimization of Die Casting Process for Aluminum Alloy Front Cover of Automobile Engine
- Delia Wu/CAMEL
- Dec 18, 2020
- 5 min read
Updated: Jul 27, 2021
With the rapid development of the automobile industry, light-alloy materials are increasingly used in parts and components due to the requirements of lightweight bodies. Aluminum alloys (such as aluminum-silicon series alloys) have the characteristics of low density, low thermal expansion coefficient, and good friction properties, and are widely used in automobile engine covers, gearbox housings, and other castings. This topic uses Magma software to analyze the filling and solidification process of the aluminum alloy front cover of a family car engine; through the analysis of the results of numerical simulation, an optimization plan for the die casting process is proposed, which provides a reference for the production of similar products.
Casting Model And Material
1. Casting model
The outer dimension of the engine front cover is about 470 mm×310 mm×105 mm, the product mass is about 3.4 kg, the average wall thickness of the main body is 3.3 mm, and the maximum wall thickness reaches 26 mm (the part marked in the wireframe is the thicker wall). The product structure is relatively complex, with a considerable number of bolt holes and reinforcing ribs distributed inside; and the wall thickness of the casting is very different, and stress concentration is likely to occur during the die casting process, resulting in uneven density, resulting in casting deformation, shrinkage, and shrinkage porosity. . The casting product model is shown in Figure 1.
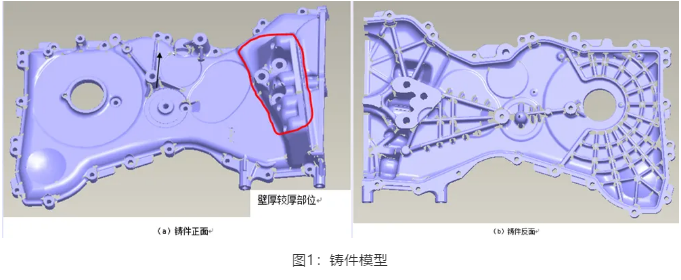
2. Casting materials
The front cover of the engine is required to have good mechanical properties and high density, and no internal defects such as cracks, shrinkage porosity, pores, and shrinkage holes are allowed. Based on the above working environment and requirements, the AlSi9Cu3 aluminum alloy is selected, which has good fluidity and excellent die casting performance. Table 1 is its chemical composition and mechanical properties.
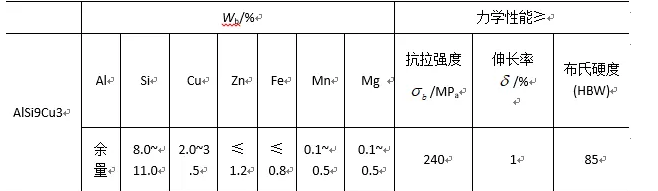
Initial Die Casting Process Plan
1. Design of initial pouring system
According to the characteristics of the product structure, it is planned to design 2 branches with a total of 6 inner runners for feeding, as shown in Figure 2. The aluminum alloy liquid is introduced into the sprue from the sprue cup, and then enters the 6-way internal gate through the 2-way branch, and finally enters the cavity for filling.
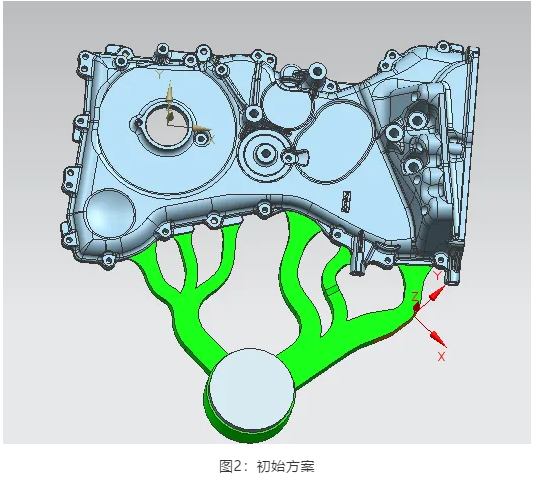
2. Determination of process parameters
The casting material is AlSi9Cu3, and the mold is DIEVAR. According to the physical characteristics of the two materials, combined with the die-casting process design manual and production experience, and through calculations, the following die-casting process parameters are determined: the initial temperature of the casting is 670℃, and the initial temperature of the mold is 180℃ ; The casting mass is 3.4 kg, the pouring system mass is 2 kg, the overflow system mass is 850g, and the total mass is 6.25 kg. The projected area of the casting is 1 196 cm2, and the total projected area is 1 554 cm2; the injection specific pressure is selected as 60MPa, and the safety factor is 1.2.
3. Simulation analysis of the preliminary plan
In order to understand the filling and solidification of the casting during the casting process, Magma software is used for numerical simulation, as shown in Figure 3. It can be seen that the filling time of the entire cavity is about 0.076 s. The initial filling speed of the molten metal entering the cavity is faster, and the filling speed of the middle area is significantly faster than the two sides. In the middle of filling, the molten metal gradually enters the thicker wall area. It was observed from time to time that the thicker-walled area was filled relatively slowly and gas stagnation was easy to occur. After the filling of the area was completed, due to higher temperature and longer solidification time, internal quality problems such as pores and shrinkage holes were prone to occur.

Die Casting Process Optimization Design
1. Optimized design of gating system
In view of the relatively slow filling of thick-walled areas, in order to ensure the quality of the castings and make the filling speed of each area basically the same during the forming process, it is proposed to add two gate feeds to the thick-walled areas to speed up the filling speed of this area, Which makes the entire filling process more stable and smooth, is more conducive to the elimination of gas and avoids shrinkage, shrinkage and other defects. Figure 4 shows the optimized scheme, and the wireframe part is a 2-way gate with added feed. Since the gate position has a large drop from the bottom of the casting, in order to make the feeding of this area smooth, a slider is added to the gate here, as shown in Figure 5, to ensure that the aluminum liquid fills the area well.
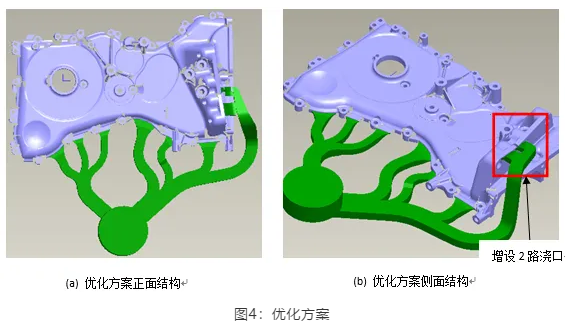

2. Simulation analysis of optimization plan
In order to verify the filling effect and solidification of the optimized scheme, numerical simulation was performed again to observe the filling and solidification process of the optimized scheme. The simulation process is analyzed from the aspects of filling temperature field change, air pressure change, solidification situation, and so on. It is found through observation that the entire cavity filling process is about 0.071 s, which is very close to the theoretical estimate. During the filling process, the molten aluminum advances relatively smoothly, and the speed is basically the same; the gas discharge in the cavity is smooth, the air pressure is relatively stable, and within the risk control range, there is no obvious gas stagnation and entrainment. In the solidification process, except for the thicker areas, the cooling and solidification are slower, and the solidification and cooling of other areas are basically uniform and ideal.
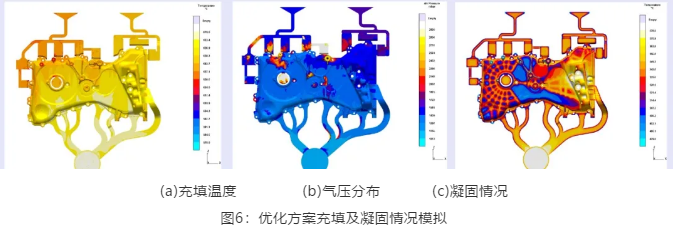
Local Area Cooling Scheme
1. High-pressure point cooling technology
High-pressure point cooling technology has been increasingly used in the die casting industry in recent years. The cooling water is adjusted to the ideal pressure state by the high-pressure point cooler, and the corresponding pipe is quickly passed through the mold to achieve the purpose of cooling. Since the core cooling rate is fast in this process, shrinkage holes will not be formed near the core position. Therefore, the use of high-pressure spot cooling technology can achieve mold heat balance, effectively improve local pore defects, greatly increase mold life, and reduce core replacement and Overhaul rate, and better guarantee the quality of castings.
2. High pressure point cold in the local area
In view of the slow cooling and solidification of the thicker part in the numerical simulation analysis process, high-pressure spot cooling is considered to be used to quickly cool the key areas to ensure the quality of the castings.
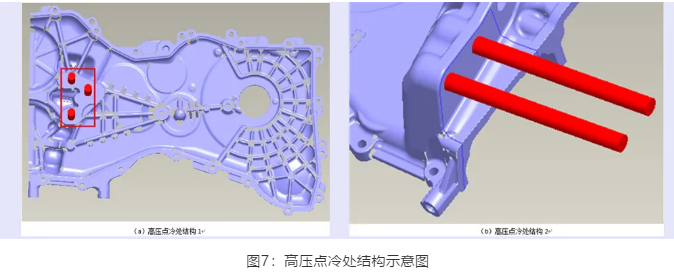
Mold Development And Trial Production
Die casting molds were developed according to the optimized process plan and trial production was carried out. The trial production was carried out on the DCC1250T horizontal die casting machine. The mold structure is shown in Figure 8. The initial temperature of the trial mold is 180°C. During the trial production process, as the injection progresses, in the low-speed injection stage, the molten aluminum enters the runner through the sprue, then enters the cavity smoothly from the inner gate, and quickly enters the high-speed injection stage. High-pressure spot cooling is performed in key areas to make the solidification time of each part of the casting basically consistent. Figure 9 is a photo of the trial product. It can be seen that the surface of the casting is smooth, the outline is clear, the quality of the inner hole is good, and there are no obvious defects. The product has been tested for airtightness and mechanical properties. After inspection, the pass rate of the product has reached 96%, and the test results meet the performance requirements.

In Conclusion
(1) Using Magma software, the filling and solidification process of the gating system and the overflow system of the aluminum alloy front cover of a certain family car engine were simulated. The corresponding problems were found through the simulation analysis, and the die casting process optimization program was proposed.
(2) After determining the relevant die casting process parameters, the optimized filling and solidification process was simulated again, and the temperature field changes, air pressure changes, and solidification conditions were analyzed, and the rationality of the optimized scheme was initially verified.
(3) Aiming at the problems of excessively high local temperature and long cooling time of castings, high-pressure spot cooling is used to speed up the cooling rate of local areas and improve the quality of castings.
Comments