Temperature Controller For Die Casting Production
- Delia Wu/CAMEL
- Jan 6, 2021
- 3 min read
Updated: Jul 27, 2021
The automatic control of die casting temperature controller is an indispensable means in modern die casting technology. What is the function of the die casting hot die machine in the temperature control of die casting?
First, The Die Casting Temperature Controller In The Preheating Stage Of Die Casting
1. Preheating the mold can reduce the number of hot modules, improve production efficiency and reduce waste;
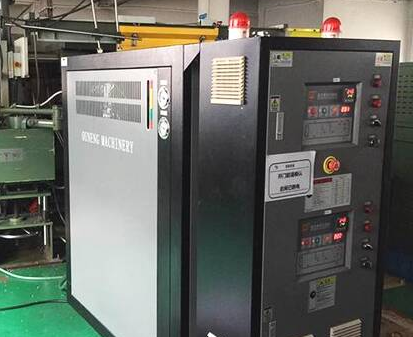
2. Preheating the mold can reduce the thermal impact of the alloy metal liquid on the die casting mold, prolong the time for the mold to generate thermal fatigue cracks, and extend
3.Preheating the mold can make the clearance of the sliding part of the mold expand and adjust, prevent the liquid metal from drilling into the sliding part, and block the mold; Preheating die by die casting temperature controller can effectively reduce the thermal modulus and thermal shock of molten metal. It is often used in gravity metal mold. The die casting hot die machine can preheat the die evenly and has the function of cooling the die to ensure the stability of the die temperature and minimize the thermal shock of the molten metal. It is the standard equipment for the production of aluminum alloy thin-walled parts and magnesium alloy casting dies.
Second, The Die Casting Temperature Controller Of The Die Casting Mold Temperature Control
If the mold temperature is too high or too low, it will cause disadvantages such as unstable casting size, high reject rate, and reduced output. When casting thin-walled castings, the heat sent to the mold is often less than the heat lost from the mold, so that the appropriate molding temperature cannot be reached, and the die casting hot mold machine needs to continuously add heat to maintain the mold temperature constant.
As far as the mold temperature is concerned, the influence on the quality of die casting has the following items.
Low mold temperature can cause:
(1) The core sticking pressure is too large, and the casting is difficult to the mold;
(2) The spray function of the spray agent deteriorates;
(3) There is a cold lap on the casting surface;
(4) The temperature difference between the mold and the liquid metal is too large, which accelerates the damage of the mold;
(5) There are patterns or marks on the mold surface;
(6) Undercast.
Excessive mold temperature can cause:
(1) Sticky mold and deformation;
(2) The consumption of spray agent increases, and the decomposition is accelerated;
(3) The cycle of die casting is prolonged;
(4)The movable part of the mold is easy to break down and accelerate wear;
(5) There are air bubbles on the surface;
(6)There are shrinkage holes inside.

Die casting temperature controller generally uses oil as the medium, and the working temperature can reach 320 ℃. But there are exceptions, such as the hot chamber die casting machine and the cooling of some cores. In order to prevent fire, pressurized water can be used as the medium, which does not vaporize at 140 °C. The non-pressurized water cooling system can only be used in places below 95 °C.
In the die casting process, the pouring temperature, filling time, casting pressure, and mold temperature. These parameters are closely related to the quality, yield, and die life of die castings. In the production of die casting, the die casting temperature controller improves the quality and process of die casting by stabilizing the temperature, and its role and effect are self-evident.
Komentarze