Stable, Like a CAMEL
Important Notice:
Our company name is "Shenzhen Camel Die".
Please note that "Camel Die" is a separate entity and is not affiliated with us in any way. Our email address is @cameldie.com
We urge our customers and partners to verify the correct contact information to avoid any confusion or miscommunication.
PROJECT MANAGEMENT SYSTEM


1. Request For Quote (RFQ)
Provide quotations within 24 hours after receiving a detailed RFQ, with preliminary die layout.
Quote information:
a) 2D/3D part data. (necessary)
b) Quantity of cavity/cast requirement.
c) Steel requirement.
d) Die casting machine.

2. Design For Manufacturing (DFM)
Provide DFM within 2 working days.
We do the DFM for each die casting dies, we analyze the parting line, gate and overflow, ejection and some potential concerns, etc. in the part analysis report.

3. Flow Simulation & FEM
Three experienced simulation technicians.
We do the Simulation & FEM for each die casting dies, we carry out filling, temperature, solidification, and cycle simulations on request, such simulations enable the establishment of casting-optimized geometries during the development phase of a part. We examine the strength of particularly stressed die components such as holder blocks and the locking surfaces of highly loaded slides during the design process.Flow3D as simulation and calculation software.
4. Mold Design
15 experienced engineers for design and 3D modeling. We provide the mold design within 3-4 working days.
From the first concept study to the finished die, our 3d die design is based on customer specifications. Interfaces: X-T, IGES, and STEP. CAD systems: Siemens NX.
5. Engineering Work
Fast response time and flexible service, Communicate in English with customers directly.
The entire process chain at a glance by ERP system, to guarantee the lead-time on time.
We have many years of experience of exporting die casting die, and our strong engineering team can provide effective suggestions of the development process from castability optimization of the desired castings, and the knowledge and understanding behind each of the individual phases of the development process flow into every other working step in the creation of a die-casting die.
Weekly Schedule (Every Monday).
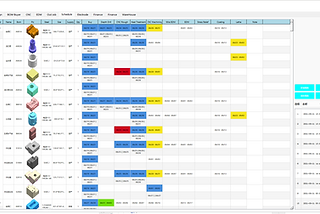

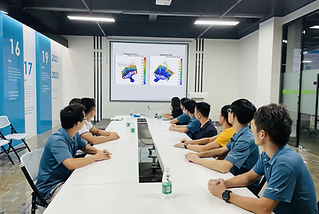(4).jpg)
6. Quality Control
3 qualified measuring technicians in 2 separate shifts.
To guarantee the mold quality and lead time on time, we do the inspection for each step in-house from material to machining.
HEXAGON for precise measurement (CMM), HEXAGON for precise measurement (Profile Projector);
Hardness testing machine, Microscope, Ultrasonic Inspection.
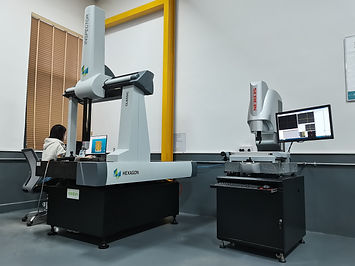.jpg)
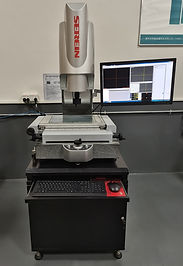.jpg)
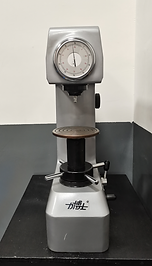







7. Sampling
Provides a trial report and video clip within 24 hours after completing the trial.
In order to ensure the dimensional accuracy of the dies before delivery to our customers, we have the capacity and the know-how to carry out dies samples independently.
For this, we are available: Sampling aluminum, magnesium, and zinc castings.
Use infrared thermography to confirm if the mold temperature is good enough to start the trial, avoid the risk of mold crack from sampling in Unsuitable temperatures.
8. Inspection Report
3 qualified measuring technicians in 2 separate shifts.
Upon customer request, we can produce initial sample test reports in-house with full documentation.
In order to perform such inspections, we employ:
HEXAGON for precise measurement (CMM) HEXAGON for precise measurement (Profile Projector)
9. Maintenance
Preventive and planned tool maintenance.
Customer service and assistance in finding the correct solution to a given problem Introducing changes or optimizations from a design to an already completed die Our goal:
Helping our customers maintain problem-free mass production;
Production stability and thus cost reduction for our customers;
Maximum utilization of tool life.


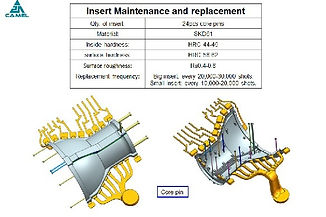
10. Shipment & After Service
Provide international service through agencies in different parts of Europe, North America, and Australia.
Check each mold to ensure all the mold requirements are completed correctly.
Sends photos with each mold shipment within 24 hours of the mold being shipped and follows the transportation progress until the mold reaches our customer.
Regularly follows up with customers to ensure the mold is running smoothly during production, and remind the customer to do tempering in time.
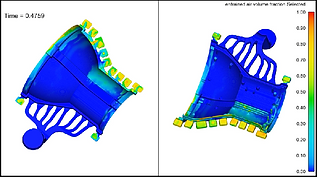





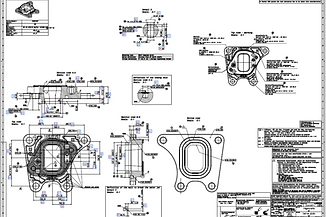
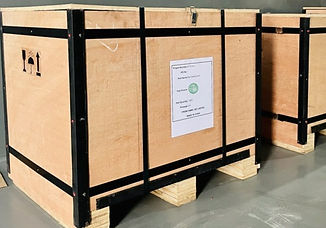
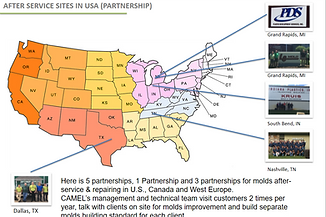
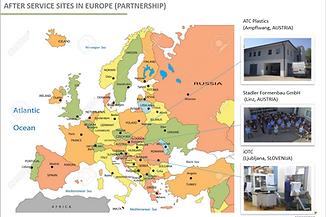