Stable, Like a CAMEL
Important Notice:
Our company name is "Shenzhen Camel Die".
Please note that "Camel Die" is a separate entity and is not affiliated with us in any way. Our email address is @cameldie.com
We urge our customers and partners to verify the correct contact information to avoid any confusion or miscommunication.
Steps Of Die Casting Die(HPDC Mold) Design
Die casting mold design, We often said as the design of die casting dies or die casting die design. Also, Which be called die casting mould design in some countries.
The basic steps are summarized as follows:
1. Understand and determine the task
2. Design preparation
3. Select the parting surface and die casting system
4. Choose the die casting equipment
5. Determine the appropriate mold structure and draw the mold assembly sketch *
6. Calculation and verification of relevant parameters *
7. Draw the die casting mold pattern *
8. Proofreading and review *
9. Organize and archive design materials
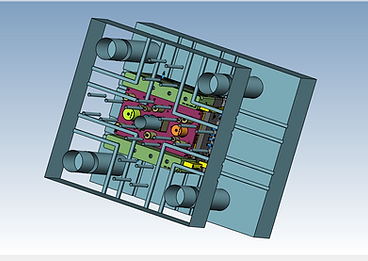
We will introduce each step in detail. It was divided into three web pages to share and now introduces steps 1-3 of die casting mold design on this page.
STEPS OF DIE CASTING DIE(HPDC MOLD)DESIGN I
1. Understand and determine the task
The task book of die-casting parts is usually given by the part designer, providing a formal part drawing after review and signing, and explaining the grades and performance requirements of the die-casting alloy materials, the use requirements or technical requirements of the die-casting parts, the production quantity and the delivery of the die-casting parts Delivery period, etc. The mold design task book is generally proposed by the die-casting parts technician according to the task book of the die-casting part, and the mold designer uses the die-casting part-task book and the mold design task book as the basis to design the mold.
2. Design preparation
1) Collect relevant information
Collect and sort relevant parts design, die-casting process, die-casting equipment, mechanical processing, and special processing materials for use in mold design. Understand the melting of die-casting raw materials and die-casting process parameters. Digest the process data, analyze whether the die casting method, equipment model, material specification, mold structure type, and other requirements proposed in the process task book are appropriate, whether the die casting equipment of the die casting production unit, the processing capacity and equipment conditions of the die processing unit can be implemented. Die-casting materials should meet the strength requirements of die-casting parts and have good fluidity, uniformity, isotropy, and shrinkage. According to the purpose of die-casting parts, die-casting materials should meet the requirements of electroplating metal conditions, decorative properties, necessary mechanical properties, or weldability.
2) Structural analysis of die castings
Digest the drawings of die-casting parts, understand the purpose of the parts, and analyze the technical requirements of die-casting parts such as manufacturability and dimensional accuracy. For example, what are the requirements for die-casting parts in terms of appearance and performance, whether the geometric structure of die-casting parts, slope inserts, etc. are reasonable, the allowable degree of die-casting defects such as flow marks, shrinkage holes, and porosity, whether there is a coating, Electroplating, machining, etc? Select the dimension with the highest dimensional accuracy of die-casting parts for analysis, and see if the estimated die-casting tolerance is lower than that of die-casting parts, and whether die-casting parts can be die-casted.
Specifically including
(1) Under the condition of satisfying the structural strength of die castings, a thin-walled structure should be adopted. This not only reduces the weight of die casting but also reduces the thermal load of the mold. The wall thickness of die castings should be uniform, avoid hot spots, reduce local heat concentration, and reduce thermal fatigue of mold materials.
(2) All corners of die-casting parts should have appropriate casting fillets to avoid the formation of edges and corners in the corresponding parts of the mold, resulting in cracks and corners.
(3) Narrow and deep cavities should be avoided as far as possible on die castings, so as not to cause sharp splits in the corresponding parts of the mold, which will deteriorate the heat sink and cause fractures. When the die castings have smaller size round holes, they can only be on the surface of the casting. Press the punching hole position of the sample, and then post-process the die-casting part.
3. Select the parting surface and die casting system
According to the basic principles of selecting the parting surface, the position of the parting surface is reasonably selected, and the number and distribution of the cavity are determined according to the structural characteristics of the die-casting part, and the form of the gating system is selected reasonably so that the die-casting part has the best die-casting forming conditions and the longest The mold life and the best mold machining performance.